Strath UAV
Undercarriage
There are several important factors to take into consideration when developing the main undercarriage for the aircraft. The most obvious of these are that the undercarriage itself must be structurally robust enough to withstand the dynamic loading experienced during landing, and that these loads can be dissipated into the fuselage without structure failure. Another important consideration is the location of the undercarriage relative to the centre of gravity and the tail plane. For the aircraft to successfully complete its rotation during take-off, the force induced by the tail plane and elevator must generate a moment sufficient to overcome the moment induced by the centre of gravity in order to allow the aircraft to rotate about its rear axle.
The main undercarriage design was initially made from sheet aluminium. However, the design of the undercarriage evolved throughout the project into a carbon fibre structure. In order to manufacture this, a hot wire foam cutter was used to achieve the desired shape. This was then covered using a carbon sock, and carbon tape applied to the upper and lower faces of the undercarriage to increase structural rigidity.
The front undercarriage was designed to absorb the impact and transmit it in a smoother way. It consists in a bended wire which has the objective of protect the electronics from the front fuselage.

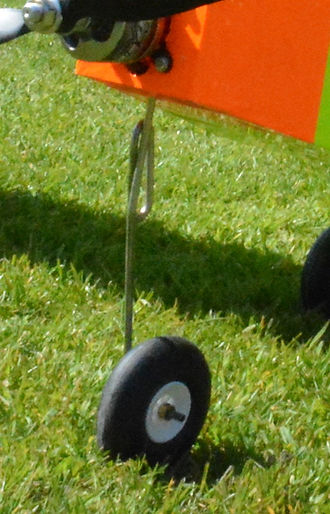